Table of Contents
Merits Of Using A Welding Wire Spooling Machine
Welding HORIZONTAL WIRE SPOOLING MACHINE is essential tools for any welding operation, as they offer a wide range of benefits that can improve efficiency, productivity, and overall quality of work. These machines are designed to spool welding wire onto a reel or spool, making it easier to feed the wire into the welding machine during the welding process. By using a welding wire spooling machine, welders can save time and effort, reduce waste, and ensure a more consistent and reliable weld.
One of the key benefits of using a welding wire spooling machine is the time-saving aspect. Spooling welding wire manually can be a time-consuming and tedious task, especially when dealing with large spools of wire. A spooling machine can quickly and efficiently spool the wire onto the reel, saving valuable time that can be better spent on actual welding work. This can help increase productivity and allow welders to complete more projects in less time.
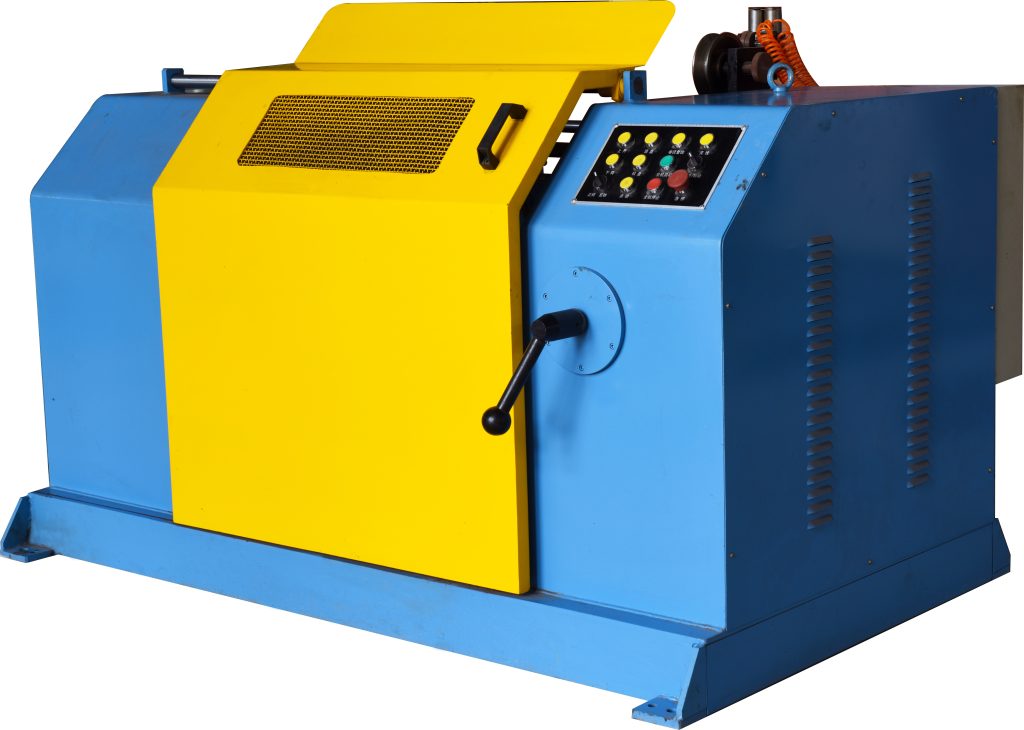
In addition to saving time, welding wire spooling machines can also help reduce waste. When spooling wire manually, there is a higher risk of tangling, kinking, or damaging the wire, which can result in wasted material. A spooling machine ensures that the wire is spooled evenly and securely, reducing the risk of waste and ensuring that every inch of wire is used efficiently. This can lead to cost savings and a more sustainable welding operation.
Another benefit of using a welding wire spooling machine is the improved consistency and quality of the weld. When welding wire is spooled manually, there is a higher chance of inconsistencies in the wire feed, which can result in uneven welds or defects. A spooling machine ensures that the wire is fed smoothly and consistently, resulting in a more uniform and reliable weld. This can help improve the overall quality of work and reduce the need for rework or repairs.
Furthermore, welding wire spooling machines are designed to be user-friendly and easy to operate. Most machines come with adjustable settings for wire tension, speed, and spool size, allowing welders to customize the spooling process to their specific needs. This flexibility can help improve efficiency and ensure that the machine is suitable for a wide range of welding applications. Additionally, many spooling machines are compact and portable, making them easy to transport and use in different work environments.
Overall, the benefits of using a welding wire spooling machine are clear. These machines can save time, reduce waste, improve consistency and quality, and offer user-friendly operation. By investing in a welding wire spooling machine, welders can enhance their welding operation and achieve better results in less time. Whether working on small projects or large-scale productions, a spooling machine can be a valuable tool for any welding operation
How To Properly Maintain And Troubleshoot A Welding Wire Spooling Machine
Welding wire spooling machines are essential tools in the welding industry, used to feed welding wire into welding machines. Proper maintenance and troubleshooting of these machines are crucial to ensure smooth and efficient operation. In this article, we will discuss how to properly maintain and troubleshoot a welding wire spooling machine.
Regular maintenance is key to keeping a welding wire Respooling Bobbin Machine in good working condition. One of the most important maintenance tasks is to regularly clean the machine. Dust, dirt, and debris can accumulate on the machine over time, causing it to malfunction. Use a soft brush or cloth to remove any buildup on the machine, paying special attention to the wire feeding mechanism.
In addition to cleaning, it is important to regularly inspect the machine for any signs of wear and tear. Check for loose or damaged parts, such as belts, gears, and bearings, and replace them as needed. Lubricate moving parts regularly to prevent friction and ensure smooth operation.
Another important maintenance task is to regularly check the tension of the wire spool. Improper tension can cause the wire to feed unevenly, leading to poor weld quality. Adjust the tension as needed to ensure a consistent feed of welding wire.
In addition to regular maintenance, it is important to troubleshoot any issues that may arise with the welding wire spooling machine. One common issue is wire feeding problems. If the wire is not feeding properly, check for any obstructions in the wire feeding mechanism and clear them if necessary. Adjust the tension of the wire spool to ensure a smooth feed of welding wire.
Another common issue is wire tangling. If the wire becomes tangled on the spool, stop the machine immediately and carefully untangle the wire. Check for any sharp edges on the spool that may be causing the wire to tangle and smooth them out if necessary.
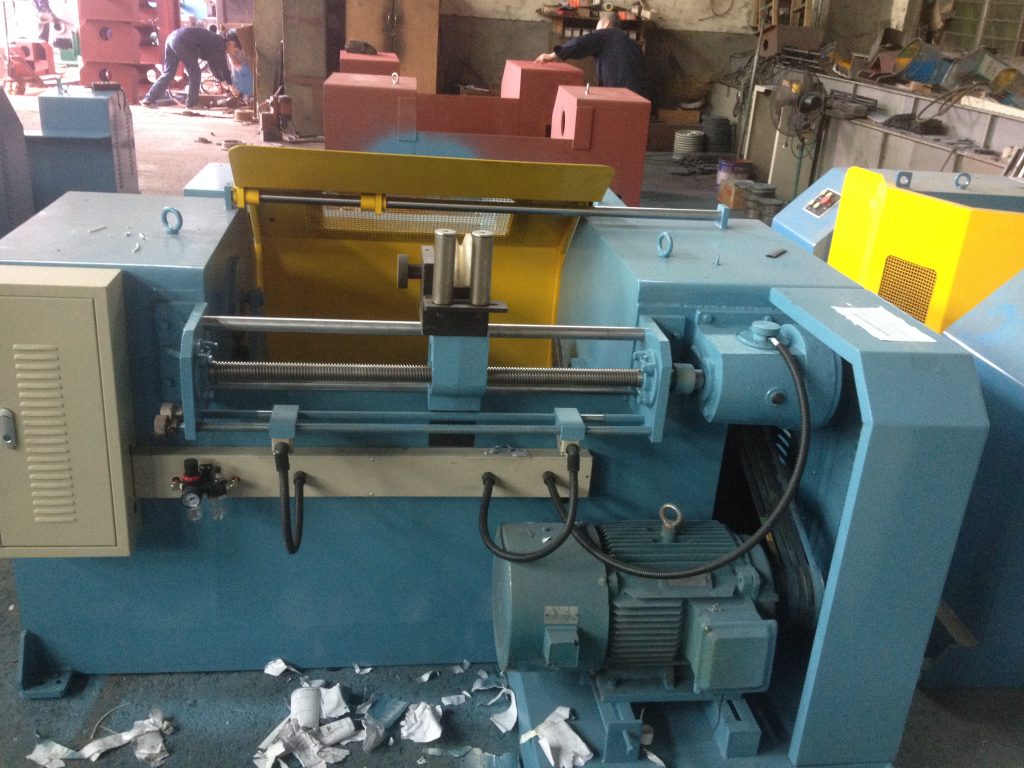
If the machine is making unusual noises or vibrations, it may be a sign of a more serious issue. Stop the machine immediately and inspect it for any loose or damaged parts. If you are unable to identify the source of the problem, contact a professional technician for assistance.
In conclusion, proper maintenance and troubleshooting are essential for keeping a welding wire spooling machine in good working condition. Regular cleaning, inspection, and lubrication are key to preventing issues and ensuring smooth operation. If any issues do arise, it is important to address them promptly to prevent further damage to the machine. By following these tips, you can keep your welding wire spooling machine running smoothly and efficiently for years to come.