വെൽഡിംഗ് വയർ മെഷീൻ ഉപയോഗിക്കുന്നതിൻ്റെ പ്രയോജനങ്ങൾ
Welding is a crucial process in various industries, from construction to automotive manufacturing. It involves joining two or more metal pieces together by melting them and allowing them to cool and solidify, creating a strong bond. One essential component of the welding process is the welding wire, which acts as a filler material to help create a strong and durable weld. In recent years, advancements in technology have led to the development of welding wire machines, which have revolutionized the welding process in many ways.
One of the primary benefits of using a welding wire machine is increased efficiency. Traditional welding methods often involve manually feeding the welding wire into the welding torch, which can be time-consuming and labor-intensive. Welding wire machines automate this process, feeding the wire continuously and consistently, allowing for a smoother and more efficient welding operation. This not only saves time but also reduces the risk of human error, resulting in higher quality welds.
Another advantage of using a welding wire machine is improved precision. These machines are equipped with advanced technology that allows for precise control over the feeding speed and wire placement, ensuring that the welding wire is deposited exactly where it is needed. This level of precision is crucial in achieving strong and reliable welds, especially in applications where accuracy is paramount. Additionally, welding wire machines can be programmed to adjust the feeding speed and wire placement based on the specific requirements of the welding job, further enhancing precision and consistency.
In addition to efficiency and precision, welding wire machines also offer increased safety benefits. Welding can be a hazardous process, with risks of burns, fumes, and electric shock. By automating the wire feeding process, welding wire machines reduce the need for manual handling of the welding wire, minimizing the risk of injury to the welder. Furthermore, some welding wire machines are equipped with safety features such as automatic shut-off mechanisms and protective guards, further enhancing workplace safety.
Furthermore, welding wire machines can help reduce material waste and costs. By controlling the feeding speed and wire placement, these machines ensure that the right amount of welding wire is used for each weld, minimizing waste and reducing material costs. Additionally, the consistent and precise welds produced by welding wire machines require less rework and touch-up, further reducing material waste and saving time and money in the long run.
Overall, the benefits of using a welding wire machine are clear. From increased efficiency and precision to improved safety and cost savings, these machines offer a range of advantages that can enhance the welding process in various industries. As technology continues to advance, welding wire machines will likely become even more sophisticated and versatile, further improving the quality and efficiency of welding operations. Whether you are a professional welder or a manufacturing company looking to streamline your welding process, investing in a welding wire machine is a smart choice that can yield significant benefits in the long run.
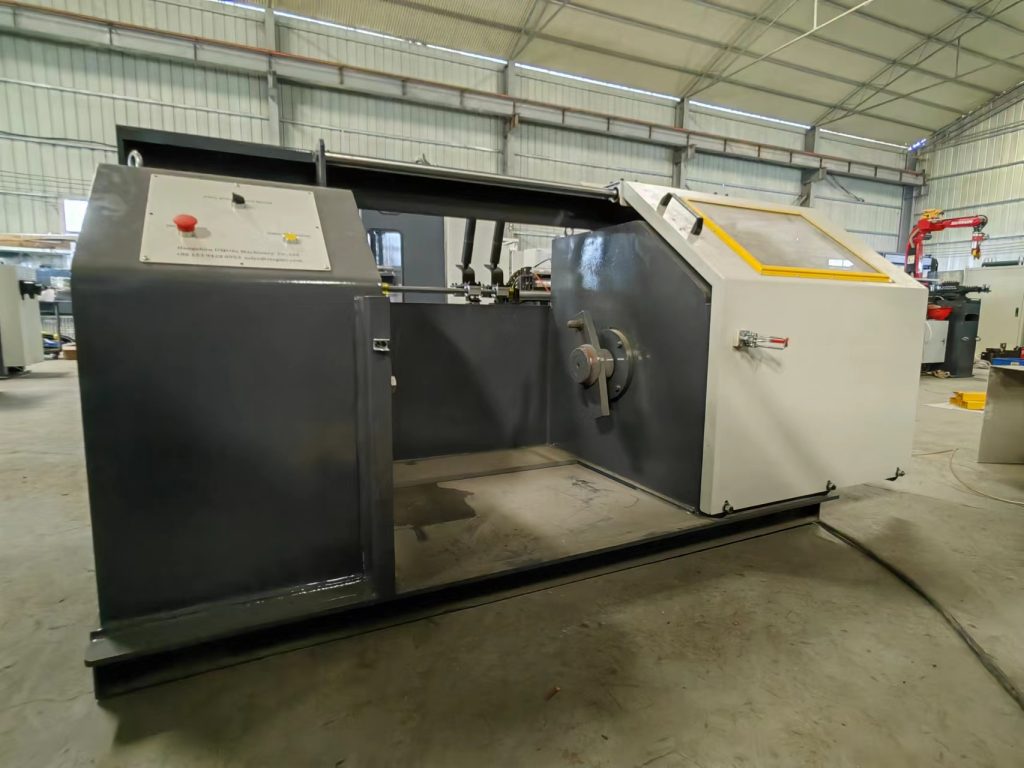